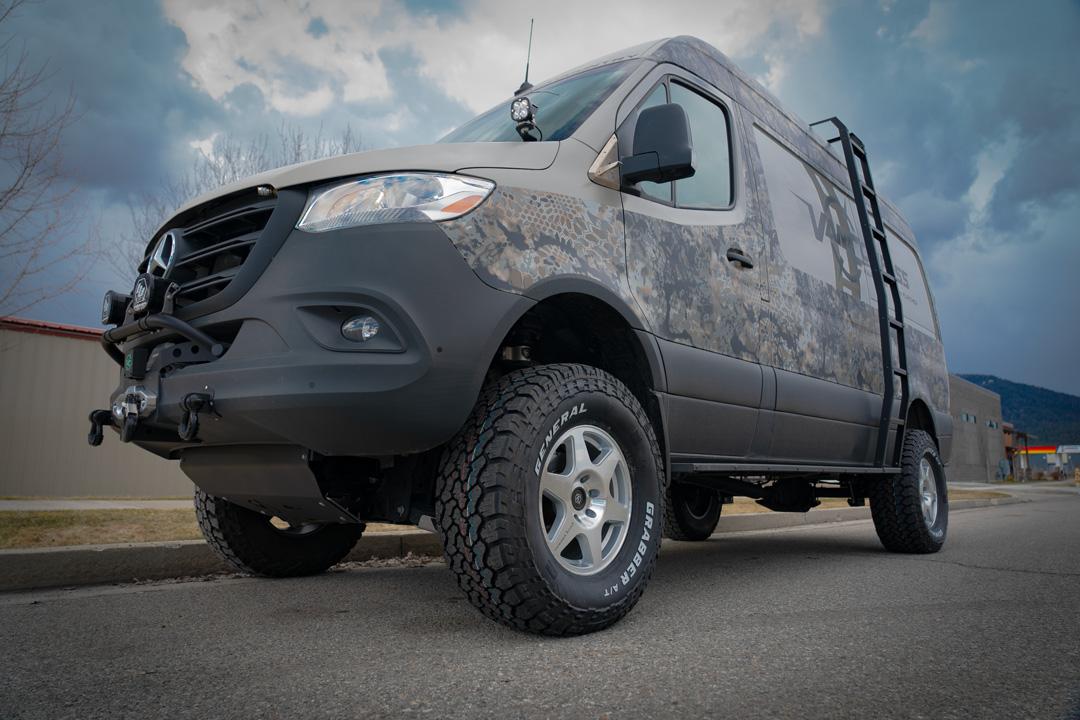
Introducing ALL NEW Wheels from Van Compass
ICONIC STYLE, FRESH FITMENT Van Compass is proud to release our new line of wheels! Drawing on traditional looks, we wanted to bring a fresh take to the van segment with timeless, iconic style. Each bold wheel design is available in 3 distinct but muted finishes that will pair with any build or aesthetic. These wheels are in stock and ready to ship! Sized in...